CIM - Ceramic injection molding process with dynamic mold temperature
Ingénierie et Architecture
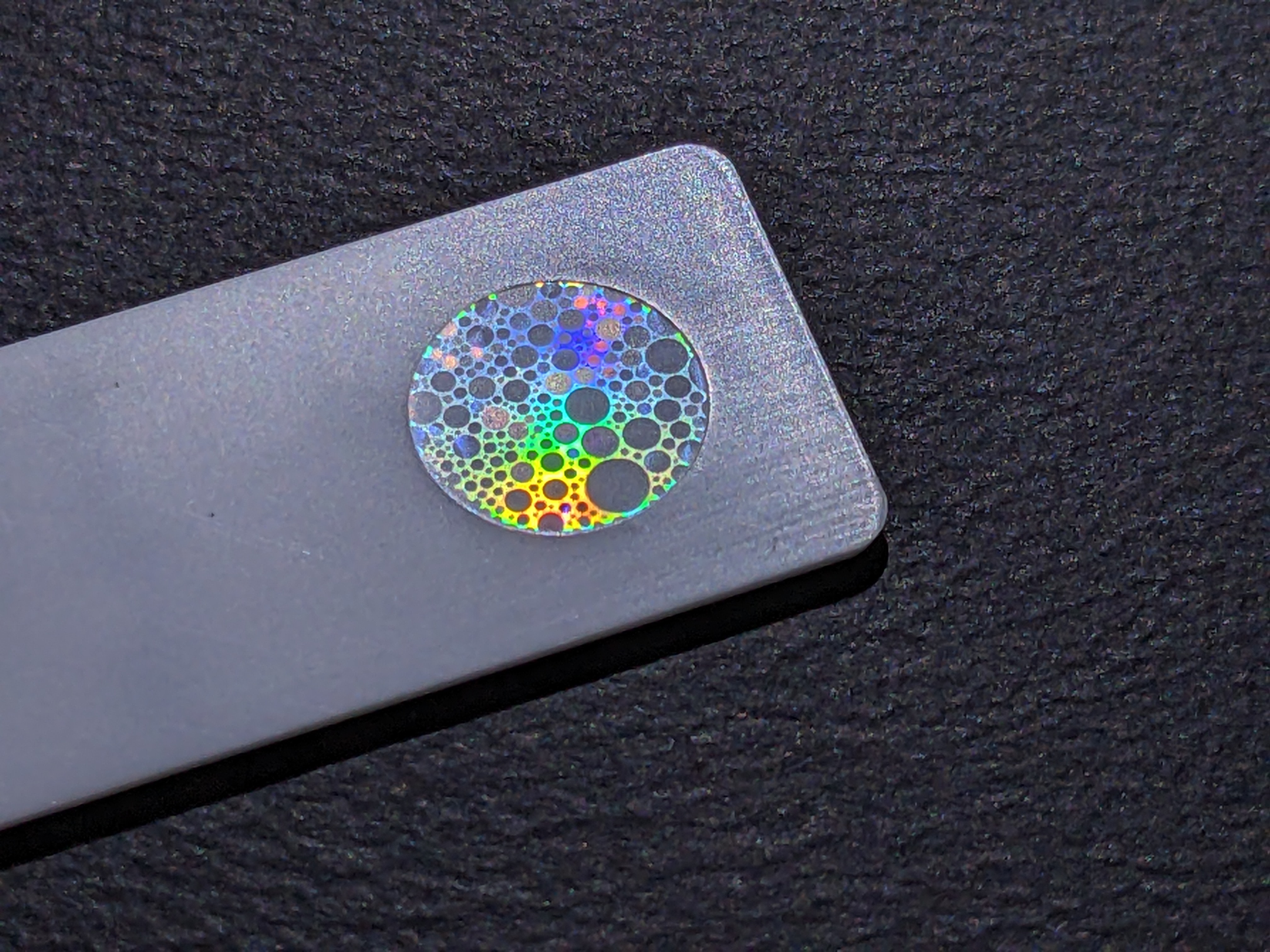
Le procédé d’injection céramique (CIM – Ceramic Injection Molding) présente aujourd’hui des limites au niveau de la faisabilité de composants en céramique. Ceci est principalement lié par rapport à la haute viscosité et le refroidissement rapide de la matière céramique injectée (feedstock). Il est donc difficile de réaliser des pièces à parois minces de quelques dixièmes d’épaisseur ou de répliquer des microstructures à partir d’une cavité moule. Également, des problèmes de qualité comme la formation de fissures ou gauchissement de pièces sont souvent rencontrés.
Dans le cadre du projet Innosuisse, nommé CIM++ (57563.1 IP-ENG), Ceramaret, Primaform et l’institut iRAP de la HEIA-FR ont visé de dépasser les limites actuelles du procédé d’injection céramique standard en intégrant deux technologies : le variotherm ainsi que le conformal cooling.
Contrairement au moulage standard qui est effectué à une température de moule constante (isotherme), le variotherm se distingue par une gestion dynamique de la température du moule. C’est-à-dire avant la phase d’injection, le moule est d’abord chauffé à une température proche à la masse céramique injectée e, après de nouveau refroidi pour l’éjection de la pièce.
Un refroidissement de moule variotherm a permis de fortement augmenter les longueurs d’écoulement et de réaliser des composants à parois très fines (0.3 mm). La qualité des pièces injectées a pu être également augmentée par une forte réduction du gauchissement. Il a été possible de reproduire des microstructures en dessous du micron, telles que des hologrammes (voir image). Les réplications obtenues correspondaient à celles de la texture originale du moule. Cette excellente qualité de réplication, aujourd’hui impossible de réaliser avec le procédé CIM standard, démontre le potentiel qu’apporte le variotherm afin d’intégrer des structures fonctionnelles ou décoratives sur des pièces céramiques injectées/frittées. Le fait de chauffer le moule diminue le « choc thermique » entre le feedstock et la cavité du moule, donc avoir une température de moule proche de la température de fusion du feedstock évite un refroidissement prématuré et améliore la qualité des pièces.
Le conformal cooling a permis d’avoir une répartition de température uniforme dans la cavité du moule. Ceci a été atteint par des canaux de refroidissement intégrés qui s’adaptent à la géométrie complexe de la cavité d’un moule. L’impact positif d’une répartition de température moule plus uniforme a également démontré une meilleure stabilité dimensionnelle et un gauchissement fortement réduit des pièces frittées.